What is Manual Handling?
Manual handling refers to the physical tasks that involve using one's body to lift, lower, push, pull, carry, or move objects. These tasks can encompass a wide range of activities, from lifting a heavy box to adjusting the position of a patient in a healthcare setting. Manual handling is prevalent across various industries and job roles, and it can present risks to the health and safety of individuals involved in these tasks.
Effective manual handling techniques are essential to prevent injuries and reduce the risk of musculoskeletal disorders, such as strains and sprains. To ensure safe manual handling, individuals should be trained in proper lifting and handling techniques, understand their physical limitations, use appropriate equipment like trolleys or hoists when necessary, and be aware of ergonomic principles to minimise strain on the body.
Manual handling safety is a significant concern in workplaces, and employers often have legal obligations to assess and manage the risks associated with manual handling activities to protect the well-being of their employees. These safety measures can include providing training, implementing ergonomic equipment and workstations, and creating guidelines and protocols to promote safe practices when handling objects or people manually.
What Kind of Jobs Might Require Manual Handling?
Many jobs across various industries involve manual handling tasks. These jobs require individuals to lift, move, or manipulate objects or people physically.
Some common examples of jobs that frequently require manual handling include:
- Healthcare Workers: Nurses, orderlies, and patient care assistants often need to lift and reposition patients, transfer them between beds and chairs, and move medical equipment.
- Warehouse and Distribution Workers: Employees in warehouses and distribution centres are responsible for loading and unloading cargo, stacking shelves, and moving heavy packages.
- Construction Workers: Construction labourers, bricklayers, and carpenters routinely lift and carry building materials, tools, and equipment.
- Retail Workers: Stock clerks, delivery personnel, and cashiers may need to move and arrange merchandise, particularly in larger retail stores.
- Manufacturing Workers: Factory workers involved in assembling products, operating machinery, and transporting materials may engage in manual handling.
- Agricultural Workers: Farmers and agricultural labourers often need to lift heavy objects, such as bales of hay or bags of feed.
- Movers and Removalists: Professionals who assist with moving household or office items are engaged in extensive manual handling activities.
- Transportation Workers: Truck drivers, bus drivers, and baggage handlers must load and unload cargo, luggage, and passengers' belongings.
- Waste Collection Workers: Those who work in sanitation or waste collection handle bins, containers, and waste materials, which involves manual lifting.
- Hospitality and Catering Staff: Kitchen staff, servers, and catering personnel handle supplies, food, and equipment, requiring manual handling.
- Gardening and Landscaping Workers: Tasks like planting, digging, and lifting heavy materials are common in this profession.
- Postmen and Couriers: These workers carry and deliver packages and mail, often requiring manual handling.
- Emergency Services Personnel: Police officers, paramedics, and firefighters may need to lift and transport injured individuals during emergency situations.
It's crucial for individuals in these professions to receive proper training in safe manual handling techniques to reduce the risk of injuries, strains, and musculoskeletal disorders associated with these physically demanding tasks. Employers also have a legal responsibility to assess and manage the risks of manual handling activities in the workplace to protect the health and safety of their employees.
How Can I Keep Myself Safe When Handling Items Manually?
Before Handling or Lifting:
Think about where the load will be placed back down and clear any obstacles that could get in the way. If you’ll be walking a longer distance with the load, consider where you could rest midway with it on a table or bench.
Once you’ve thought about the lift, you should get into a stable position with your feet apart and one leg slightly forward and get a good hold of the item or load. You should try to hold it as a close to your body as you can rather than just holding it with your hands.
It’s important that you start any lift with a good posture, slightly bending your back as well as your hips and knees before handling the items or load.
During Handling of Items:
You should try and keep any load close to your waist for as long as possible while lifting, keeping the heaviest side next to your body. You should also avoid looking down if possible and keep your head looking up and forward.
Try to move smoothly while carrying loads and avoid any sudden movements that could increase the risk of injury. If you’re struggling to do this, the load is probably too heavy for one person and you should ask for help.
When Items are Put Down:
When placing items back down, bend your back, knees and hips only slightly and slowly put the load on the ground. If the load needs to be put in a precise area, put it down first and then adjust its positioning.
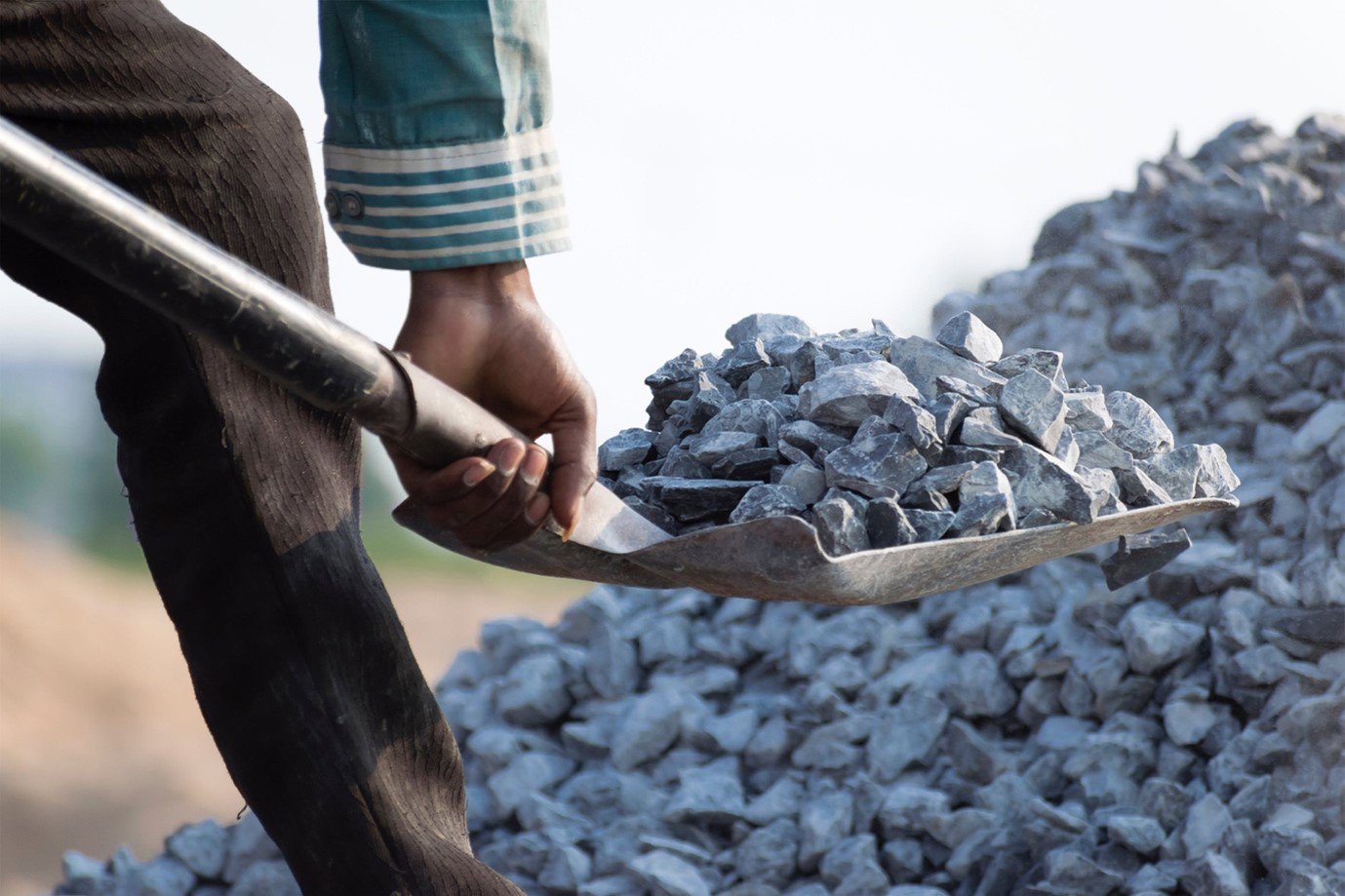
What Should my Employer be Doing to Keep me Safe?
Under the Manual Handling Operations Regulations 1992, your employer has a duty to reduce the possibility of you sustaining a manual handling injury in the workplace. In the first instance, this means they should prevent you from having to manually handle items wherever possible. But where it is necessary, they should:
- Make a suitable and sufficient assessment of manual handling operations – employers must look at the risks of each manual handling task, considering the capability of individuals as well as the nature of each load and the wider working environment.
- Take steps to reduce the risk of injury to employees carrying out manual handling jobs – this could include providing adequate training for all employees or rearranging storage areas to minimise the distances that items need to be carried.
- Provide employees with information – where it’s considered reasonably practical to do so, employees should be given precise information on the weight of the items or loads they’re handling as well where the centre of gravity is likely to be if this is not positioned centrally.
If you think your employer has failed to put the above safety measures in place and you’ve suffered a manual handling accident as a result, you could be entitled to compensation and rehabilitation support.
What factors should be considered during any lifting task?
There are various manual handling tasks that your employees may be engaged in, which encompass activities like lifting, lowering, pushing, pulling, and carrying.
However, each lifting task is unique, and as a result, there are specific considerations that must be addressed, including:
Individual Capability: Recognising that each employee possesses unique physical abilities and may have different health conditions, it's important to assess the capabilities of every worker before assigning manual handling tasks. This assessment helps mitigate the risk of injuries or other related issues.
The Nature of the Load: Loads can vary greatly in weight and shape. While one load might be heavier, another could be awkwardly shaped and challenging to handle. Depending on the characteristics of the load, it's essential to determine whether an employee can manage it independently or if they require assistance, such as the use of a forklift truck.
Environmental Conditions: Several environmental factors must be taken into consideration before commencing a manual handling activity. This includes factors such as lighting, temperature conditions, and the presence of slippery floors, all of which can impact the safety and success of the task.
Training: Manual handling training is legally mandated in situations where staff are engaged in lifting, lowering, pulling, or pushing tasks that carry a certain level of risk. The purpose of this training is to ensure that employees understand the potential hazards associated with manual handling and are equipped with the knowledge to reduce the risk of injuries.
I’ve Been Injured at Work – Can I Make a Claim?
We understand that the circumstances surrounding an accident at work aren’t always “black and white” and you might be unsure about whether you’re eligible to make an accident at work claim for compensation.
When you first contact us, our experienced Personal Injury Lawyers will offer you a free claims assessment where we’ll listen to the details of your accident and let you know if we think you have a potential claim.
If we’re able to take on your case, we’ll begin our investigation into what caused your accident and how your injuries have affected your life. We’ll carry out the latter with help from independent medical experts.
It might be the case that you need to take an extended period of time off work to recover from your injuries and this can bring its own set of financial worries. If your employer admits liability, we’ll work to secure you interim payments, so you won’t need to worry about paying any immediate costs while you recuperate.
It’s important to remember that it’s ultimately your right to claim compensation for an injury in the workplace, and your employer should have insurance in place to cover this. To find out more, get in touch with our friendly and approachable Personal Injury Solicitors.